Welding Lead: The Backbone of Precision Welding
Understanding Welding Leads and Their Role in High-Performance Welding Tasks
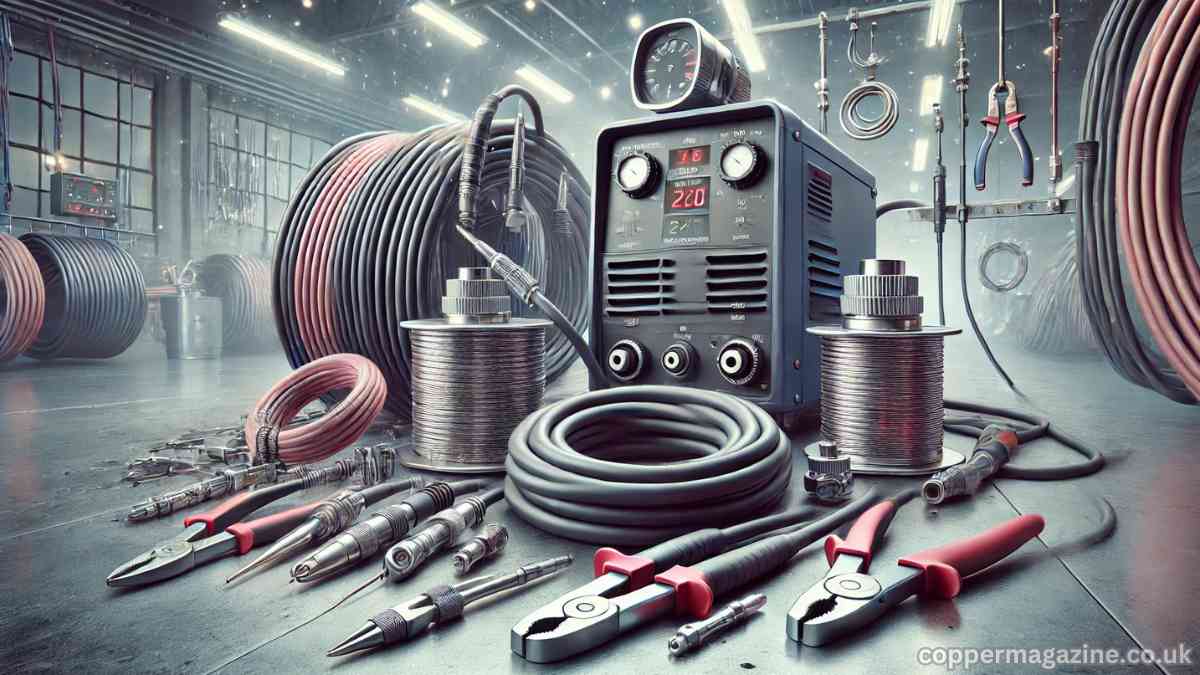
Welding leads are essential components in welding operations, enabling seamless current transmission and ensuring optimal performance in various welding applications. Whether you are a professional welder or a hobbyist, understanding welding leads and their associated components is vital for achieving efficiency and precision. In this article, we will delve into the core aspects of welding leads, their types, and how to select the perfect one for your needs.
What is a Welding Lead?
A welding lead is a specialized cable designed to transmit the electrical current necessary for welding. These leads connect the welding machine to the electrode holder and the workpiece, creating a circuit for the welding process. Made from high-conductivity copper strands and durable insulation materials, welding leads are designed for flexibility and safety.
Key Components of Welding Leads
- Cable:
- The cable forms the backbone of a welding lead, made of fine copper strands that ensure excellent conductivity and flexibility.
- The insulation, typically crafted from high-grade rubber or synthetic polymers, protects the cable from environmental hazards and electrical damage.
- Electrode Holder:
- This component securely grips the welding electrode and connects to one end of the welding lead, allowing for controlled arc welding.
- Ground Clamp:
- The ground clamp attaches to the workpiece, completing the circuit required for effective welding operations.
Different Types of Welding Cables
Several types of welding cables are available, each suited to specific welding needs. Below are the most commonly used options:
- 1/0 Welding Cable:
- Ideal for heavy-duty welding tasks requiring high amperage over moderate distances.
- Commonly used in industrial applications due to its excellent current-carrying capacity.
- 2/0 Welding Cable:
- Suitable for high-demand welding operations, this cable supports extended distances while maintaining current efficiency.
- 4/0 Welding Cable:
- Designed for extremely heavy-duty applications, the 4/0 cable is capable of handling significant current loads, often exceeding 400 amps.
- Welding Lead Wire:
- A smaller yet efficient wire, often used for lighter tasks or within compact welding setups.
Factors to Consider When Selecting a Welding Lead
Selecting the right welding lead is essential to ensure safety, durability, and optimal performance. Consider the following factors:
- Amperage Requirements:
- Ensure the welding lead can handle the maximum amperage of your welding machine. For example, a 1/0 welding cable is ideal for applications requiring up to 300 amps, while a 4/0 welding cable is suitable for heavier loads.
- Length of the Cable:
- The longer the cable, the greater the voltage drop. To minimize losses, opt for thicker cables for extended distances.
- Environmental Conditions:
- Choose welding cables with robust insulation to withstand harsh conditions such as extreme heat, abrasion, or exposure to chemicals.
- Flexibility:
- Welding often involves intricate movements. A flexible welding lead wire ensures ease of handling and precision in tight spaces.
- Welding Lead Reels:
- Reels are essential for organized storage and easy deployment of welding leads. They prevent tangling and extend the lifespan of the cables.
Importance of Welding Lead Reels
Welding lead reels are indispensable accessories that enhance the usability and durability of welding cables. They:
- Keep the cables organized and prevent damage caused by improper storage.
- Allow for quick deployment and retraction, saving time during setup and teardown.
- Protect the insulation from wear and tear, ensuring a longer service life.
Safety Tips for Using Welding Leads
- Inspect Regularly:
- Regularly check for wear, cuts, or exposed wires to prevent electrical hazards.
- Use Appropriate Insulation:
- Ensure the insulation on your welding lead wire is intact and suitable for the working environment.
- Avoid Overloading:
- Always use a cable rated for the machine’s maximum amperage to prevent overheating.
- Proper Storage:
- Utilize welding lead reels to store cables safely, preventing kinks and extending their lifespan.
Applications of Welding Leads
Welding leads are versatile and used in various fields, including:
- Industrial Manufacturing:
- Heavy-duty welding operations in factories and workshops.
- Automotive Repairs:
- Essential for welding tasks in vehicle fabrication and repair shops.
- Construction:
- Widely used in building sites for structural welding tasks.
- Hobbyist Projects:
- Lightweight welding lead wires are perfect for DIY and small-scale projects.
Maintaining Your Welding Lead
Proper maintenance ensures the longevity and efficiency of your welding lead:
- Clean Regularly:
- Remove dirt and grease from the cables to maintain good conductivity.
- Inspect Connections:
- Tighten loose connections and replace worn-out electrode holders or clamps.
- Store Properly:
- Use welding lead reels for safe and efficient storage.
Conclusion
Welding leads, including essential components such as welding cables, welding lead wires, and welding lead reels, play a crucial role in the welding process. From light-duty 1/0 welding cables to heavy-duty 4/0 welding cables, choosing the right one is critical for achieving efficient, high-quality results. With proper selection, usage, and maintenance, welding leads not only enhance safety but also ensure optimal performance for any welding application.